Main Applications
● Cell disruption: E. coli, yeast, algae, etc.
● Nano Medicine :Lotions, fat emulsions, eye drops, inhalants, etc.
● Food emulsion: Coenzyme Q10 microcapsules, vitamin microcapsules, sea buckthorn microcapsules, oat protein, etc.
● Cosmetics/Medical Beauty:collagen, hyaluronic acid, essence, lotion, functional liposome (ceramide, astaxanthin, salicylic acid)
Fine chemicals/new energy materials: CMP polishing slurry, conductive polymers, nano-oxide dispersion, hydrogen fuel cell catalysts, graphene, carbon black, carbon nanotubes, conductive slurry dispersion
Main Features
● Special design of feeding valve allows direct feeding without exhaust.
● Equipped with high-precision pressure sensor and digital display panel.
● Equipped with frequency conversion control system, and the flow can be adjusted according to requirements.
● Equipment material
—Adopt 316L stainless steel with high hygienic level, high-temperature resistant, wear-resistant and anti-corrosion.
—The core components are made of special ceramics, which are durable and have a long service life.
● Temperature controllable
—The inlet and outlet of the cooling joint are connected to the constant temperature bath, which effectively controls the temperature rise of the homogeneous material.
● Safety control
—Automatically cut off the controller circuit.
Working principle
Under the reciprocating motion of the plunger, the material is transported to a valve group with adjustable size, and is subjected to extremely strong compression. When passing through the current limiting slit, the material hits the valve at a very fast speed, resulting in cavitation effect, impact effect and shear effect, so that the aggregated material is evenly dispersed.
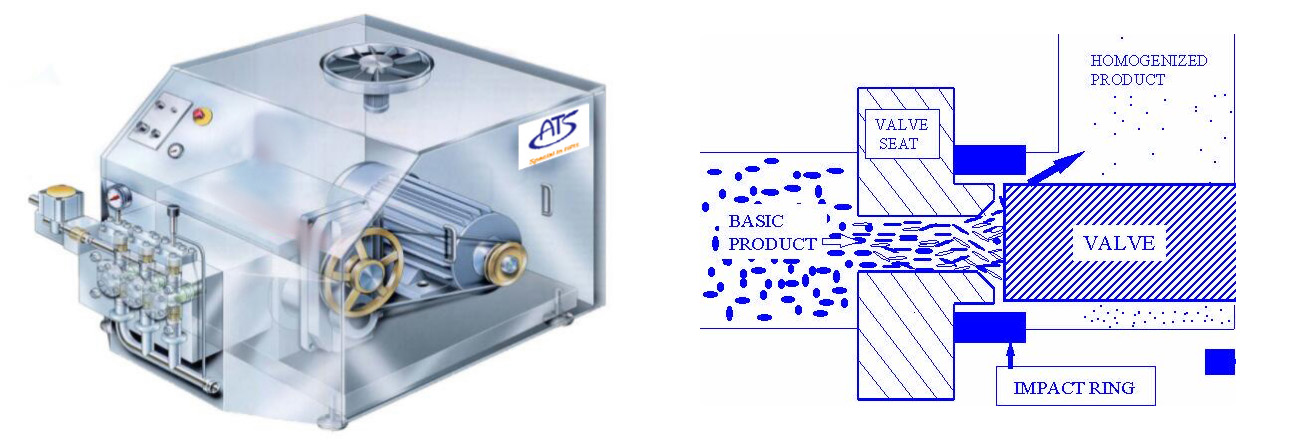